
Trill keys stuck together
Moderators: Classitar, pied_piper, Phineas
Trill keys stuck together
Trill keys will not move independently at all. A job for WD-40? Pins out? Detailed help appreciated.


Last edited by moondaddy on Tue Jul 15, 2008 10:10 am, edited 1 time in total.
-
- Posts: 2311
- Joined: Sun Jul 16, 2006 3:11 pm
It sounds like it could be several things. Make sure the screws in the posts aren't too tight. Make sure the springs arent bent. Other than that, either the trill rod needs to have the pins removed, old oil cleaned out and re-oiled and pinned.... OR.... the steel in the rod might be bent. Or the hingetube. It could be lots of things. But, if I had to guess, it seems to me it's probably just in need of oil.
Have you unpinned a flute mechanism before? If you tell us more about the work you HAVE done on this flute, it could help us assist you.
Have you unpinned a flute mechanism before? If you tell us more about the work you HAVE done on this flute, it could help us assist you.
Basically just disassembly, reassembly, cleaning, tapped those posts straight. I guess a pin or two need to come out so I can take the trill assembly apart and de-gunk it. Do I punch the pins from the underside out through the top and if only one needs to come out which would it be,
lever,
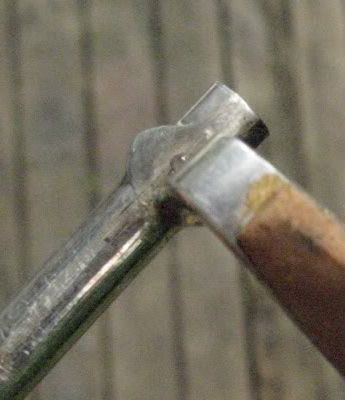
or key?
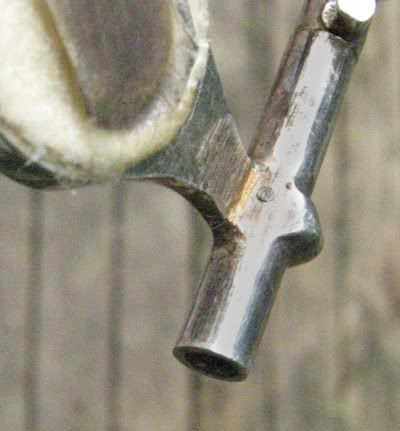
How small does the punch have to be? Any hints on making one? I have a bench grinder.
Thanks
lever,
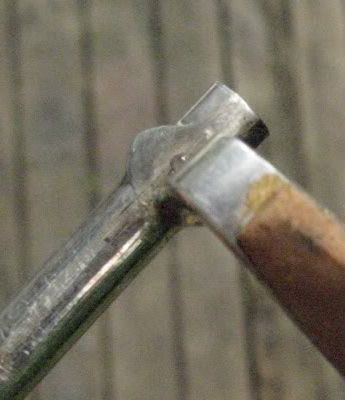
or key?
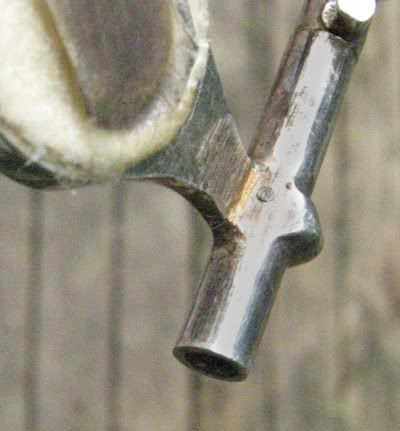
How small does the punch have to be? Any hints on making one? I have a bench grinder.
Thanks
- pied_piper
- Posts: 1962
- Joined: Sat Mar 31, 2007 1:31 pm
- Location: Virginia
On most flutes, if you take out either pin, you should be able to slide the inner/middle hinge tube off of the steel rod. If so, you don't need to remove both pins.
In a previous posting, you indicated that the trill keys would not move independently. If they are rusted so tight that they will not move at all, you might want to soak the hinge tube in penetrating oil before starting. If that doesn't do the trick, you can try gently heating the entire length of the hinge tube with a torch on low. Many times the heat will allow you to break it free.
From your pictures, it looks like the pin by the pad in the second photo may be more easily accessible. It also appears that the bottom of the pin is nice and flat, so that might be a bit easier to drive out. And, yes, you punch it out from the underside. The pin is tapered like a sewing needle, so if you try to drive it from the top, it will just drive it in tighter and overstretch the hole or possibly damage the hinge rod or steel shaft. In fact, a large sewing needle of the proper diameter and cut to the right length, is a suitable substitute if you should need to replace one of the pins.
When you drive it out, be sure to support the hinge tube directly under the pin. A small block of lead (which is softer than brass or silver) or a piece of thick leather will protect the key from getting marred and the pin can be driven into the lead or leather. If you use leather, place it on a very solid surface like an anvil or vise.
You can make a pin punch that is suitable. If you have a small piece of drill rod, that would be ideal. Otherwise, if you have an old nail punch that you are willing to sacrifice, you can grind the end to a suitable sized point. In the James Phelan book, The Complete Guide to the Flute and Piccolo, page 97 describes the process of making a pin/spring punch. He suggests grinding the the drill rod to a point of 0.025". Afterward, use a torch to heat the tip end red hot and quench it in water to harden it. Then reheat it slowly to temper it to a light straw color. It needs to be hard but not so hard that it's brittle.
In a previous posting, you indicated that the trill keys would not move independently. If they are rusted so tight that they will not move at all, you might want to soak the hinge tube in penetrating oil before starting. If that doesn't do the trick, you can try gently heating the entire length of the hinge tube with a torch on low. Many times the heat will allow you to break it free.
From your pictures, it looks like the pin by the pad in the second photo may be more easily accessible. It also appears that the bottom of the pin is nice and flat, so that might be a bit easier to drive out. And, yes, you punch it out from the underside. The pin is tapered like a sewing needle, so if you try to drive it from the top, it will just drive it in tighter and overstretch the hole or possibly damage the hinge rod or steel shaft. In fact, a large sewing needle of the proper diameter and cut to the right length, is a suitable substitute if you should need to replace one of the pins.
When you drive it out, be sure to support the hinge tube directly under the pin. A small block of lead (which is softer than brass or silver) or a piece of thick leather will protect the key from getting marred and the pin can be driven into the lead or leather. If you use leather, place it on a very solid surface like an anvil or vise.
You can make a pin punch that is suitable. If you have a small piece of drill rod, that would be ideal. Otherwise, if you have an old nail punch that you are willing to sacrifice, you can grind the end to a suitable sized point. In the James Phelan book, The Complete Guide to the Flute and Piccolo, page 97 describes the process of making a pin/spring punch. He suggests grinding the the drill rod to a point of 0.025". Afterward, use a torch to heat the tip end red hot and quench it in water to harden it. Then reheat it slowly to temper it to a light straw color. It needs to be hard but not so hard that it's brittle.
"Never give a flute player a screwdriver."
--anonymous--
--anonymous--
Great post Piper. I currently have the Phelan book (1980 ed) checked out from library. Would WD 40 work as a penetrating oil? What is drill rod anyway? Could I just grind down an old drill bit? What else would work? I have an old sewing machine needle that I could grind a new point on and use for a punch. Might that do the job?


- pied_piper
- Posts: 1962
- Joined: Sat Mar 31, 2007 1:31 pm
- Location: Virginia
WD-40 is OK to use as a penetrating oil.
Drill rod is a high-carbon hardened solid steel rod. That is generally what is used to make common drill bits and other tools where a high degree of hardness is needed. It is also frequently used to make the key shafts in musical instruments. It's available in numbered or fractional sizes like drill bits and sold by metal suppliers and musical instrument repair suppliers (i.e J.L. Smith and Ferrees). You can Goggle "drill rod" for other sources.
So, yes you can probably use a drill bit to make a punch. Just use the solid part and cut or grind off the spiral cutting section. If you have a solid piece that is at least 2-3 inches long, that should be usable to make a punch. You might need a larger size bit to get a solid piece that is long enough - you can grind the end and taper it down to a point. You just need enough length to grasp with your fingers while driving out the pin. Also, drill bits are hardened and somewhat brittle. You might heat it to temper it a bit to soften it before cutting and grinding to a point. That will save some wear and tear on the grinding wheel or file.
The sewing machine needle might work, but I think a drill bit might be better. The sewing machine needle is not solid so it may not yield a good point after grinding. Also it is probably chrome plated. That might peel off or interfere with trying to harden and temper the metal.
Drill rod is a high-carbon hardened solid steel rod. That is generally what is used to make common drill bits and other tools where a high degree of hardness is needed. It is also frequently used to make the key shafts in musical instruments. It's available in numbered or fractional sizes like drill bits and sold by metal suppliers and musical instrument repair suppliers (i.e J.L. Smith and Ferrees). You can Goggle "drill rod" for other sources.
So, yes you can probably use a drill bit to make a punch. Just use the solid part and cut or grind off the spiral cutting section. If you have a solid piece that is at least 2-3 inches long, that should be usable to make a punch. You might need a larger size bit to get a solid piece that is long enough - you can grind the end and taper it down to a point. You just need enough length to grasp with your fingers while driving out the pin. Also, drill bits are hardened and somewhat brittle. You might heat it to temper it a bit to soften it before cutting and grinding to a point. That will save some wear and tear on the grinding wheel or file.
The sewing machine needle might work, but I think a drill bit might be better. The sewing machine needle is not solid so it may not yield a good point after grinding. Also it is probably chrome plated. That might peel off or interfere with trying to harden and temper the metal.
"Never give a flute player a screwdriver."
--anonymous--
--anonymous--
I have plenty of old bits of all sizes. What would be a range of diameters of bits that would work? As for the first tempering to soften it to grind, how do I tell when it's hot enough? How do I cool it? Then after grinding do I have to temper it again to reharden it? How would I do that?
Thanks for all your help.
Thanks for all your help.
- pied_piper
- Posts: 1962
- Joined: Sat Mar 31, 2007 1:31 pm
- Location: Virginia
I'd say use one near 1/4" in size. A little bigger or smaller is OK too. You just want something that is big enough to hold easily. The bigger the size though, the more grinding you'll need to do to get a suitably sized point.
The hardness of carbon steel can be manipulated through heating and cooling. Here's a brief description. I'd recommend wearing leather gloves and eye protection for these procedures. For all of these, hold the metal drill bit by one end with a pair of pliers or visegrips.
Annealing (Softening): Heat the metal with a torch on high until it turns a bright cherry red/orange in color. (That will be about 1500-2000 degrees). If the metal is allowed to cool natually, it will cool to it's softest state.
Hardening: Heat the metal with a torch until it turns a bright cherry red/orange in color. Quench the metal in a bucket of oil or water. For most handheld tools a quart size is good. Water hardening will result in the hardest state and will be somewhat brittle. Oil will also harden, but not quite as hard and brittle as water.
Tempering: After fully hardening the metal, the hardness can be further reduced by tempering. To temper, begin to heat the metal again, but do it slowly. Don't hold the flame on the metal. Instead, "dance" the flame over the metal so that it heats gradually. You should see a gradual color change in the metal, first to a blue color (like some drill bits) and then to a straw color (like handtools). The straw color is good for a punch. Then, allow the metal to cool naturally.
You can read more here:
http://en.wikipedia.org/wiki/Carbon_steel
http://en.wikipedia.org/wiki/Heat_treatment
http://en.wikipedia.org/wiki/Tempering
Anneal the metal to soften it. Then you can cut it and grind it more easily. When you have a good point, harden the metal again. After cooling, you can temper it so that it's not so brittle. After that, you should have a good, usable pin punch.
The hardness of carbon steel can be manipulated through heating and cooling. Here's a brief description. I'd recommend wearing leather gloves and eye protection for these procedures. For all of these, hold the metal drill bit by one end with a pair of pliers or visegrips.
Annealing (Softening): Heat the metal with a torch on high until it turns a bright cherry red/orange in color. (That will be about 1500-2000 degrees). If the metal is allowed to cool natually, it will cool to it's softest state.
Hardening: Heat the metal with a torch until it turns a bright cherry red/orange in color. Quench the metal in a bucket of oil or water. For most handheld tools a quart size is good. Water hardening will result in the hardest state and will be somewhat brittle. Oil will also harden, but not quite as hard and brittle as water.
Tempering: After fully hardening the metal, the hardness can be further reduced by tempering. To temper, begin to heat the metal again, but do it slowly. Don't hold the flame on the metal. Instead, "dance" the flame over the metal so that it heats gradually. You should see a gradual color change in the metal, first to a blue color (like some drill bits) and then to a straw color (like handtools). The straw color is good for a punch. Then, allow the metal to cool naturally.
You can read more here:
http://en.wikipedia.org/wiki/Carbon_steel
http://en.wikipedia.org/wiki/Heat_treatment
http://en.wikipedia.org/wiki/Tempering
Anneal the metal to soften it. Then you can cut it and grind it more easily. When you have a good point, harden the metal again. After cooling, you can temper it so that it's not so brittle. After that, you should have a good, usable pin punch.
"Never give a flute player a screwdriver."
--anonymous--
--anonymous--
- atoriphile
- Posts: 155
- Joined: Sat Nov 11, 2006 2:35 pm
- Location: Washington, DC
- pied_piper
- Posts: 1962
- Joined: Sat Mar 31, 2007 1:31 pm
- Location: Virginia
I wish it were that cheap and easy. Pin punches are hard to find in a size small enough for flute pins.
http://www.harborfreight.com sells a set of 13 pin punches for $9.99 but the smallest size is 1/16" or 0.0625". For a flute pin, the suggested point size is 0.025" or 1/40".
There are special flute pin driver tools available from the various musical instrument tool suppliers, but they are not just a simple punch. Instead, the tool is more complex with a driver punch holder that keeps the punch properly aligned, multiple sized punches, and several different anvils to support the key rod/hinge tube. Those sell for over $100.
While making a simple pin punch might sound like a lot of work, it's really not that difficult. With a torch, grinding wheel, file, and suitable metal stock at hand, it can be completed in a half hour or so.
http://www.harborfreight.com sells a set of 13 pin punches for $9.99 but the smallest size is 1/16" or 0.0625". For a flute pin, the suggested point size is 0.025" or 1/40".
There are special flute pin driver tools available from the various musical instrument tool suppliers, but they are not just a simple punch. Instead, the tool is more complex with a driver punch holder that keeps the punch properly aligned, multiple sized punches, and several different anvils to support the key rod/hinge tube. Those sell for over $100.
While making a simple pin punch might sound like a lot of work, it's really not that difficult. With a torch, grinding wheel, file, and suitable metal stock at hand, it can be completed in a half hour or so.
"Never give a flute player a screwdriver."
--anonymous--
--anonymous--
Finally got the job done. Nephew made me 3 punches from drill stock. The sharpest one was the best although since he didn't temper them it took the point off to do the punching. Then it was just a matter of applying heat (I used a wood burning tool) and WD-40 and alcohol. Now I'm looking at pads. Just got a Yamaha clarinet with Valentino pads. Man do those give a nice seal. They make them for flute don't they?
- pied_piper
- Posts: 1962
- Joined: Sat Mar 31, 2007 1:31 pm
- Location: Virginia
Glad to hear you were successful.
I've never used the Valentino pads, but yes they are available for flute. (http://valentinopads.com/)
I'm sort of old school and prefer the traditional skin pads to the newer synthetic pads. From what I hear, they do seal well, but when playing, the feeling is a bit softer - some say almost mushy feeling. That's OK for student instruments where they get banged about. Most pro flutists prefer a firmer feel when the keys are closed.
The advantage to the synthetic pads is the durability. Since they don't have the traditional skin covering, they can take a bit more abuse.
For your purposes, either style would probably be fine.
I've never used the Valentino pads, but yes they are available for flute. (http://valentinopads.com/)
I'm sort of old school and prefer the traditional skin pads to the newer synthetic pads. From what I hear, they do seal well, but when playing, the feeling is a bit softer - some say almost mushy feeling. That's OK for student instruments where they get banged about. Most pro flutists prefer a firmer feel when the keys are closed.
The advantage to the synthetic pads is the durability. Since they don't have the traditional skin covering, they can take a bit more abuse.
For your purposes, either style would probably be fine.
"Never give a flute player a screwdriver."
--anonymous--
--anonymous--